汪曙俊1 万千里2 黄莉2 马义华2
(1.技术中心;2.汽车摩托车轴承厂)
摘 要:分析了电机用密封深沟球轴承运转温度过高的原因。提出了采用密封挡边和“过渡接触”形式解决该类轴承运转温度过高的办法,并通过试验确定了相关参数,用户使用证明效果良好。
关键词:滚动轴承;电机用密封深沟球轴承;密封结构
目前,电机已向高速、节能、静音、大功率等方向发展,如煤炭等行业所使用的防爆电机等60%以上由原来的中低速电机被高速电机所代替。公司生产的某型号电机用密封深沟球轴承被安装在这些高速电机时,普遍出现运转温度过高的现象,影响了电机的安全使用。有关人员对此进行了分析。
1 原因分析
分析认为,该密封轴承在运转时出现发热的主要原因有以下几方面。
1.1 密封结构
该轴承的密封形式为非接触式密封(2Rz),密封结构形式见图1。该密封结构含有3处密封间隙,密封曲路长度较长,但对密封所涉及的相关轴(径)向尺寸和形位公差精度要求较高,如果密封槽、密封圈的加工精度不高;或轴承轴向游隙较大,或轴承安装时内外圈端面不在同一基准平面上;或内外圈轴线不重合;或使用中存在轴向力等。
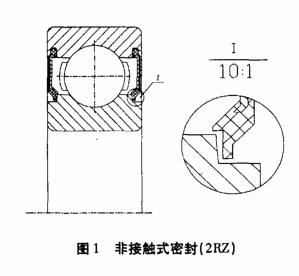
那么在游隙的影响下,内圈相对外圈将产生位移,“吃”掉密封间隙,贴近(紧)密封圈唇口端面。在轴向方向,如果密封处的轴向密封间隙小于轴向位移量,轴承将由设计时的非接触式密封转变为接触式密封,且轴向位移越大,内圈与密封圈的轴向接触压力越大,摩擦发热越严重。而与套圈轴向位移方向相反的一侧,由于密封间隙增大,密封性能下降,则容易产生润滑脂泄漏现象,过量 的润滑脂泄漏会影响轴承的润滑性能,Z终会加剧轴承的工作温度上升。
同样,在径向方向,也会由于密封槽、密封圈的加工精度不高、轴承组装不良等问题,导致内圈密封槽与密封圈在径向方向的接触。众所周知,接触式密封比非接触式密封的运转温度要高,且接触压力越大,接触区域越大,运转温度越高。
以6308E-2RZ为例,高速电机轴承选用的径向游隙为C3组,其轴向位移量可达0.2mm以上,而产品设计的轴向Z小密封间隙小于该值,即使在零件加工精度全部合格的情况下也容易产生接触。因此,轴承制造、使用中非预期密封形式的改变是造成使用运转温度过高的主要原因。
1.2 产品制造
图1结构的外圈密封槽止口和内圈密封槽的加工流程主要是车加工成型、热处理、Z后进入装配。在不考虑加工设备精度的前提下,其尺寸、形状位置精度及表面粗糙度等相对轴承其它(磨削)工作表面的加工精度较差,若再考虑热处理过程中非预期变形等因素,其累积误差与Z小密封间隙几乎相当,使得密封间隙或处于临界接触状态,或被“吃”掉变为接触,此时,若接触表面光滑或密封唇口润滑状态良好,摩擦发热不会很严重,但由于密封槽表面是车加工表面,再经过热处理后表面不同程度存在有氧化皮,使得该表面比较粗糙,因此,摩擦时阻力较大,容易产生高温。
在密封圈制造上同样也存在加工精度方面的问题,如同轴度、唇口尺寸和圆度、平面度等,都可能会导致密封圈在径向或轴向同时与内圈密封槽接触,产生摩擦发热。
除加工精度外,还有重要一点是对密封槽和密封圈的加工精度的检测,目前缺乏必要有效的检测和控制手段。由于受外圈止口和内圈密封槽空间尺寸小的限制,大部分尺寸只能采用样板的方式进行检查,且还无法实施全检,而对热处理后产生的变形即使发现有问题也缺少有效返工手段。如果要想保证套圈止口和密封槽的加工精度,完善检测控制手段,那么,在制造成本和加工效率上目前也存在一定困难。
1.3 安装使用
轴承在安装时,由于轴承座或轴的加工误差,容易引起外圈轴线与内圈轴线的不重合,或内外圈端面不在同一平面的现象,从而影响到密封间隙,若在使用中存在轴向力,则影响更大。
2 密封结构分析与选型
根据上述分析,并结合电机轴承的使用条件、产品制造条件、制造成本、制造效率等各方面因素,同时还考虑到这些因素在短期内不会得到有效改善的前提下,技术人员初步确定调整电机用轴承的密封结构。
2.1 密封结构选型
选型的基本要求:
1)工作温升和漏脂率应在标准规定内;
2)对轴承游隙、安装和轴向力的变化不敏感;
3)符合目前套圈和密封圈加工条件及所能达到的质量水平;
4)满足用户轴承的安装习惯和使用工况条件。
2.2 密封结构的确定
首先,对目前行业上深沟球轴承比较常见的密封结构进行了分析比对,从中找出适合电机轴承需要的基本密封结构形式。经过比对认为图2所示的结构基本满足要求,该密封结构的特点是:采用径向密封形式,内圈密封槽为直挡边形式,结构简单,对套圈轴向位移不敏感,而且密封挡边的加工精度高容易保证、检测方便,加工效率高。但该结构主要用于接触式密封,接触压力较大,工作时温度较高,因此,不能直接在电机轴承上应用,只有在此基础上进行调整,才能满足要求。
在密封结构基本确定后,下一步是确定密封接触型式。目前,滚动轴承的密封接触型式主要有接触式和非接触式两种基本形式,接触式密封结构密封效果好,但使用转速受一定限制,且容易发热,而非接触式的密封效果虽然不如接触式密封,但工作温升相对较低。如果能选用这两种密封接触型式各自的优点,抑制其不足就是一种比较理想的密封结构方案。通过对电机轴承的结构、制造条件、安装、使用条件等多方面的综合分析后,初步确定采用“过渡接触”这一密封接触形式,“过渡接触”是借鉴了公差配合中的“过渡配合”术语引出的。通常,接触式密封圈的唇口与内圈密封槽在径向或轴向有一定的压缩量(一般为0.1mm-0.8mm),类似于公差配合的过盈配合,而非接触式密封圈的唇口与内圈密封槽有一定间隙量(0.4mm-1.0mm),类似于公差配合的间隙配合。“过渡接触”则介于传统的接触式和非接触式之间,根据密封圈和密封挡边的尺寸精度状态,以及内外圈安装后的状态,其密封圈的唇口与内圈密封槽(挡边)的 “配合”状态可以存在三种:小间隙不接触、小压缩量接触、部分接触部分不接触,其接触状态与公差配合的“过渡配合”类似。
考虑到电机轴承的使用环境、密封圈的制造水平和制造成本,以及密封圈在轴承内部的轴向(空间)位置等,密封圈采用单唇结构。
为了减少接触压力,在密封圈唇部设置减压槽(见图2),以增加密封唇的弹性和在内外圈轴线不重合时柔性调节的能力。
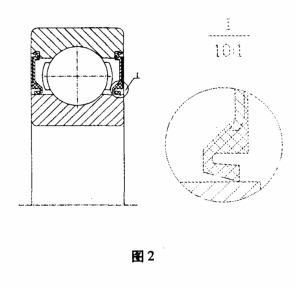
3 试验验证
3.1 试验内容
1)在保证温升、漏脂率合格的前题下,确定轴承密封圈唇口直径尺寸。
2)在标准填脂量条件下确定Z佳填脂量和填脂方式。
3)密封结构改进前后的性能对比。
根据对密封结构的初步设计和上述要求,单独制造了一批轴承用于试验,并通过更换不同唇口直径尺寸的密封圈和填加不同填脂量形成若干试验组进行试验。
3.2 试验和判定依据
试验依据:JB/T857l《滚动轴承 密封深沟球轴承防尘、漏脂、温升试验规程》
判定依据:JB/T7752《密封深沟球轴承 技术条件》
3.3 试验结果
1)密封圈唇口直径尺寸试验
试验采用6308新设计的密封结构。为了减少误差,试验样本由一组(8套)轴承和4组(每组8 套)不同密封唇口直径尺寸的密封圈组成,4组(A、B、C、D组)试验样本的填脂量相同,润滑脂采用2号低噪音锂基润滑脂(下同),采用人工定量注脂,然后分别安装在同一台试验机上进行试验。
试验结果(略)显示:4组试验样本的温升均低于标准值(非接触式≤45℃),温升范围为33℃~40℃,其中B组Z低,但4组试验样本中有部分样本存在漏脂率超标的现象,试验分析认为此与填脂量较多有关。
试验基本确定采用唇口直径尺寸为B组的密封圈。
2)Z佳填脂量试验
试验仍采用以上试验已经用过的轴承,但密封圈使用B组尺寸,并根据标准填脂量(5.5-13.8克)将填脂量分为4组。
试验结果(略)显示:在试验温升基本相同的情况下,填脂量超出x值以上的两组试验样本绝大部分出现了漏脂率超标的现象,而小于x值以下的两组试验样本漏脂率全部合格。
考虑到密封轴承的使用寿命主要取决于润滑脂的寿命,而在密封轴承密封性能(温升、漏脂、防尘等)能够保证的前题下,充足的润滑脂量对润滑性能和寿命有利等因素,因此,确定新设计的6308轴承的Z佳填脂量x值,但在制造时允许在该值的基础上进行“浮动”。
3)密封结构改进前后的性能对比
选用原6308-2RS密封结构与6308新密封结构轴承各8套,两组轴承的填脂量相同,在同一台试验机上进行试验。
试验结果(略)显示:新、老密封结构的漏脂和温升性能均满足要求,但新密封结构的温升性能好于老密封结构。
4)填脂方式试验
选用B组密封圈6308新密封结构轴承8套,填脂量根据标准理论填脂量分为4组,其中单面填脂和双面填脂方式各两组。
试验结果(略)显示:在Z佳填脂量条件下,填脂方式对漏脂和温升性能不会产生影响。
为了对新密封结构负责,又追加了一组试验,条件是重新换一组(8套)轴承,采用B组密封圈和Z佳填脂量,试验结果相同。
4 结论
通过对高速电机用密封深沟球轴承结构设计、工艺分析和试验验证,初步确定了高速电机用密封深沟球轴承结构及相关尺寸、Z佳填脂量和填脂方式,并将这些结果用于小批量(400套)生产发往用户装机进行使用验证,经过近半年的用户使用证明,改进后轴承使用中再未出现运转温度过高的现象,从而扭转了公司该类产品在市场呈萎缩的局面。以此为契机,将这一成果推广到6300系列 电机用密封深沟球轴承的密封结构进行系列改造,取得了较好的经济效益及社会效益。
来源:《轴承技术》2007年第2期