韩振禹
(辽宁省抚顺石化工程建设有限公司第六分公司,辽宁抚顺 113004)
摘 要:阐述了楔形环密封型罗茨风机在生产运行中存在的问题,分析了导致风机不能长周期运转的主要原因,针对设备运行中各种不利因素,对设备实行了多处改造后,提高了风机的运行稳定性,增加了聚乙烯产品的生产能力,为装置平稳生产做出了突出贡献。
关键词:罗茨风机;楔形环;热膨胀;改造;轴承箱
聚乙烯装置的GB-101罗茨风机由于输送温差大,设备经常因密封环失效,使润滑油进入风机壳体内,对输送介质产生了污染,同时也因润滑不良,造成轴承抱轴、主轴断裂等设备事故发生,严重影响了设备的平稳运转,通过对设备内部结构的改造,改善了设备的密封效果,增加了设备的运转周期,提升了输送介质的纯净度,确保了生产装置的产品质量。
1 罗茨风机的工作原理及性能参数
罗茨风机为容积式风机,输送的风量与转数成比例,叶轮端面和风机前后端盖之间及风机叶轮之间始终保持微小的间隙,在同步齿轮的带动下,风从风机进风口沿壳体内壁输送到排出的一侧,风机内腔不需要润滑油。具有高效节能,介质纯净、精度高,寿命长等特点,轴承箱与风机腔的密封有涨圈式、迷宫式、填料式及楔型环式4种形式,以输送空气为主,也可用来输送煤气、氢气、乙炔、二氧化碳等易燃、易爆及腐蚀性气体。聚乙烯装置的净化器再生风机GB-101,为DANTECLTD公司生产,技术参数为:转速1500r/min,功率37kW,壳体及转子材质均为碳钢,吸入压力185kPa,排出压力400kPa,流量1418.4m3/h,传动方式采用皮带连接,轴承箱与风机腔为楔型环式密封。
2 GB-101净化风机不稳定原因分析
当风机向反应釜供给冷风时,工作温度正常,风机运转平稳。当供热风时,工作温度急剧升高,转子温度上升达到1000-1200℃,再加上转子工作时与气体产生的摩擦热使转子的温度进一步升高,这时使转子的热膨胀量比风机简体的热膨胀量大得多,同时产生了胀差。造成移动端的楔形环间隙增大,使楔形环的封油作用大大下降。同时造成润滑油被吸入机体,导致润滑油内漏严重,使轴承及齿轮因缺油造成严重烧损等故障发生。
根据碳钢的热膨胀线型理论a=1.15x10-5m/(m•℃)
已知:转子长度LI=350mm、简体长度L2=350mm,转子温度tl=1200℃、筒体温度t2=600℃,则:
风机转子与风机简体胀差为:1.15×10-5x350x(120-60)=0.24(mm)。
根据风机结构产生的胀差方向,由风机的定位轴承(NU2308)向径向支撑轴承(NJ3308)方向膨胀,造成同步齿轮端的楔形环间隙增大(原间隙只有0.10mm)使楔形环的封气甩油、封油作用大下降。同时造成润滑油被吸入风机,油耗增加。
又由于高温的气体泄漏使润滑油温度上升,粘度下降、气化,润滑能力下降,造成齿轮和滚动支撑轴承烧毁,使风机的温度进一步上升,转子膨胀进一步增大,使转子与墙板发生摩擦。即严重的动、静摩擦,造成设备事故。
3 提高GB-101净化风机运行稳定性的措施
改造过程的技术关键在于怎样才能使楔形环在热膨胀过程中楔形间隙不变,保持在0.10~0.12之间。由于风机轴承室是镶在风机墙板内,两者之间有0.01~0.03的径向间隙。轴承室压盖通过3个M8螺丝与墙板同定,一端用SKF-NU2308双列向心球轴承定位,另一端用NSK-NJ3308短圆柱支撑轴承(膨胀端),所以才造成这一端在胀差的作用下使楔形环间隙增大,根据风机结构图可以看:
(1)膨胀端转子轴上的锁紧被帽锁固了同步齿轮间隔套NJ3308轴承内圈楔形密封环气封套和转子成为一体部件(动部件)。
(2)而轴承室和NJ3308轴承外圈由轴承室压盖螺丝压紧固定在墙板上,成为一体部件(静部件)。
为了保证楔形环的楔形间隙不变,第1步把膨胀端改为NU2308轴承,变成定位端(图1),另一端轴承不变(原定位端)也是NU2308轴承,但轴承室进行了改造使轴承室与墙板不固定,原轴承压盖的3个紧固螺丝孔由Ø9改为Ø12.5镶入3个滑动配合的短套,短套的长度比压盖厚度长出0.5mm,原压盖螺丝只起到导向止转作用,不起压紧固定轴承室的作用。
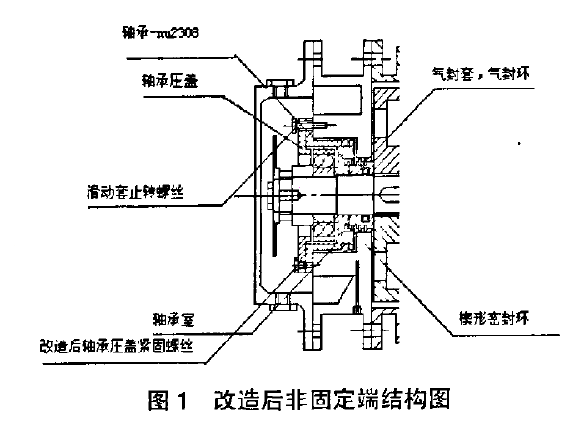
轴承的压紧是通过原轴承室3个顶丝孔的M10的内螺纹,用M10×20短螺丝通过压盖固定。这样使轴承室与轴承楔形环气封套成为一体部件。第2步为了减少风机热吹时,气体泄漏对滑油的影响,气封的气环由1道改为3道(图2)。改造后风机整体结构图(图3)。
改造后的特点:
(1)保证驱动端轴承的支撑稳定性(不窜动);
(2)原定位侧改为膨胀侧,保证了楔形环间隙不变;
(3)气封套上气封环的增加减少了气体的泄漏量;
(4)改造设计简单,原设计改动量少,易进行机械加工。
4 改造后产生的效果
设备经过改造后,运行平稳,检修频率和维修成本大幅降低,职工劳动强度得以减轻,同时也避免了润滑油进入系统中造成的介质污染,为装置降本增效、安稳长满优运行做出了突出贡献。
来源:《当代化工》2012年05期